Indroduction
Ever wonder how the medicines you take are developed? It’s a complex and fascinating journey that begins long before the pill reaches your hand. In the pharmaceutical industry, this process is known as “process development,” and it’s one of the most crucial steps in ensuring that medicines are safe, effective, and available to those who need them. Let’s dive into this vital aspect of drug production and see how it shapes the medicines we trust every day.
What Is Process Development?
Process development in the pharmaceutical industry is all about refining and perfecting the methods used to produce a drug. From the early stages of research to full-scale production, every step needs to be meticulously planned and tested. But why is this so important? Well, the quality of a drug can be affected by even the smallest changes in the production process. Imagine if a slight variation in temperature or a minor delay in mixing ingredients could alter the efficacy of your medication. Scary, right?
So, what exactly does process development involve? It’s a multifaceted approach that includes both upstream and downstream processes. Upstream processes involve everything leading up to the production phase, such as selecting the right raw materials and designing the production method. Downstream processes focus on purification, packaging, and ensuring the final product meets all regulatory standards.
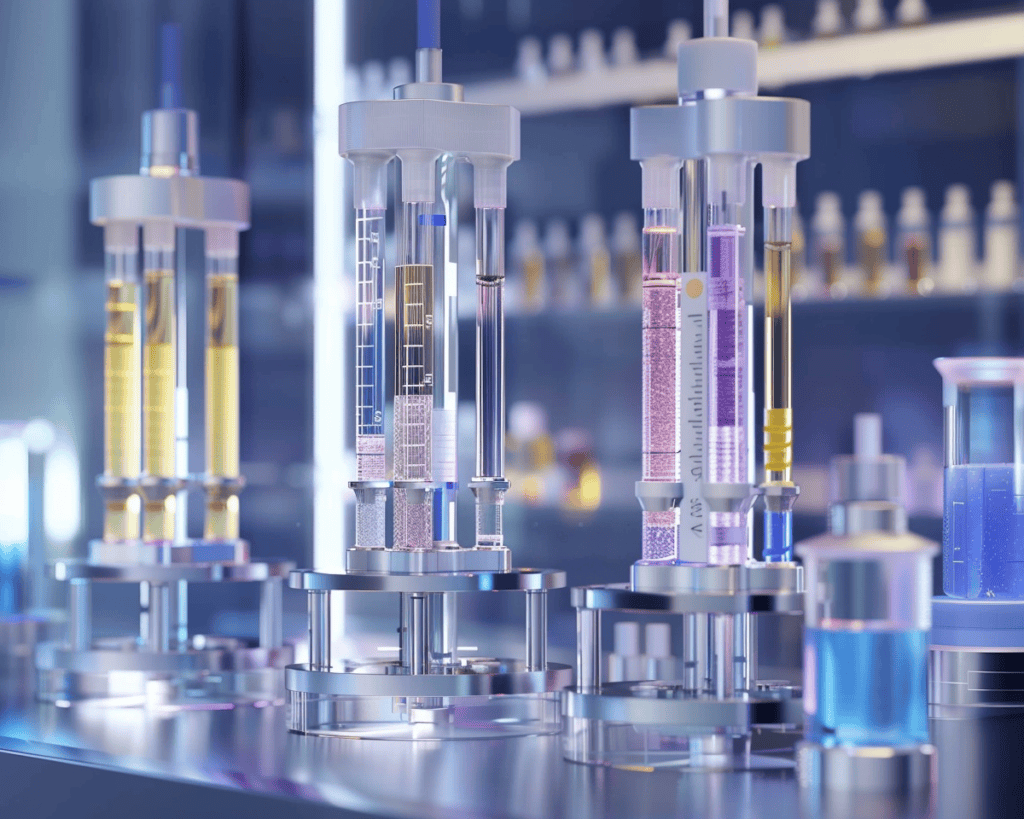
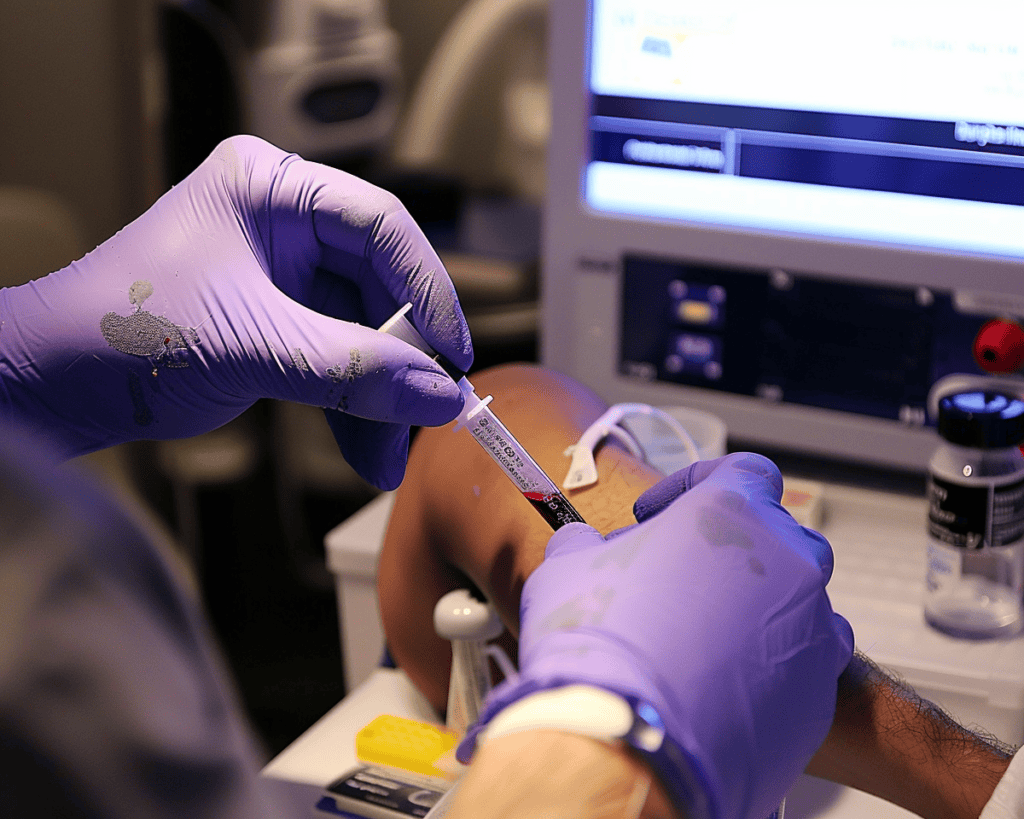
The Importance of Process Development in Drug Manufacturing
Now, you might be wondering, “Why go through all this trouble?” The answer lies in the importance of consistency and safety. Process development ensures that every batch of a drug is identical in quality, strength, and purity. Without it, the same drug might vary from one batch to another, which could be disastrous for patients relying on it.
Think about it this way: would you trust a medicine that works one day but not the next? Probably not. That’s why pharmaceutical companies invest so much time and resources into process development. It’s about creating a reliable product that doctors can prescribe with confidence and patients can take without fear.
The Stages of Process Development
Let’s break down the stages of process development. Understanding these stages can give you a clearer picture of how a drug moves from concept to reality.
1. Preclinical Development
The journey begins in the lab, where scientists conduct experiments to identify potential drug candidates. This phase involves a lot of trial and error. Researchers test various chemical compounds to see which ones have the desired effect on a particular disease. Once they find a promising candidate, they move on to the next stage.
2. Process Design
This stage is where the magic happens. Scientists and engineers work together to design a process that can be scaled up for mass production. They consider factors like the best method for synthesizing the drug, the equipment needed, and the conditions under which the process should occur. It’s like building a recipe for a cake, but instead of flour and sugar, they’re working with complex chemical compounds.
3. Process Optimization
Once a process is designed, it’s time to fine-tune it. What do I think of this stage? It’s perhaps the most challenging part. Scientists must tweak the process to ensure it’s not only effective but also efficient. This might involve adjusting temperatures, changing the order of steps, or experimenting with different solvents. The goal is to create a process that produces the highest quality product with the least waste.
4. Scale-Up and Technology Transfer
After optimization, the process needs to be scaled up for commercial production. This involves taking the process developed in the lab and applying it to a larger scale. It’s a bit like moving from baking a single cake to producing thousands of them in a factory. This stage also involves technology transfer, where the process is handed over to the manufacturing team.
5. Validation and Regulatory Approval
Before a drug can be sold, the process must be validated. This means proving that the process consistently produces a product that meets all quality standards. Regulatory agencies, such as the FDA, require extensive documentation and testing to ensure that the drug is safe and effective. Only after receiving regulatory approval can the drug be mass-produced and distributed.
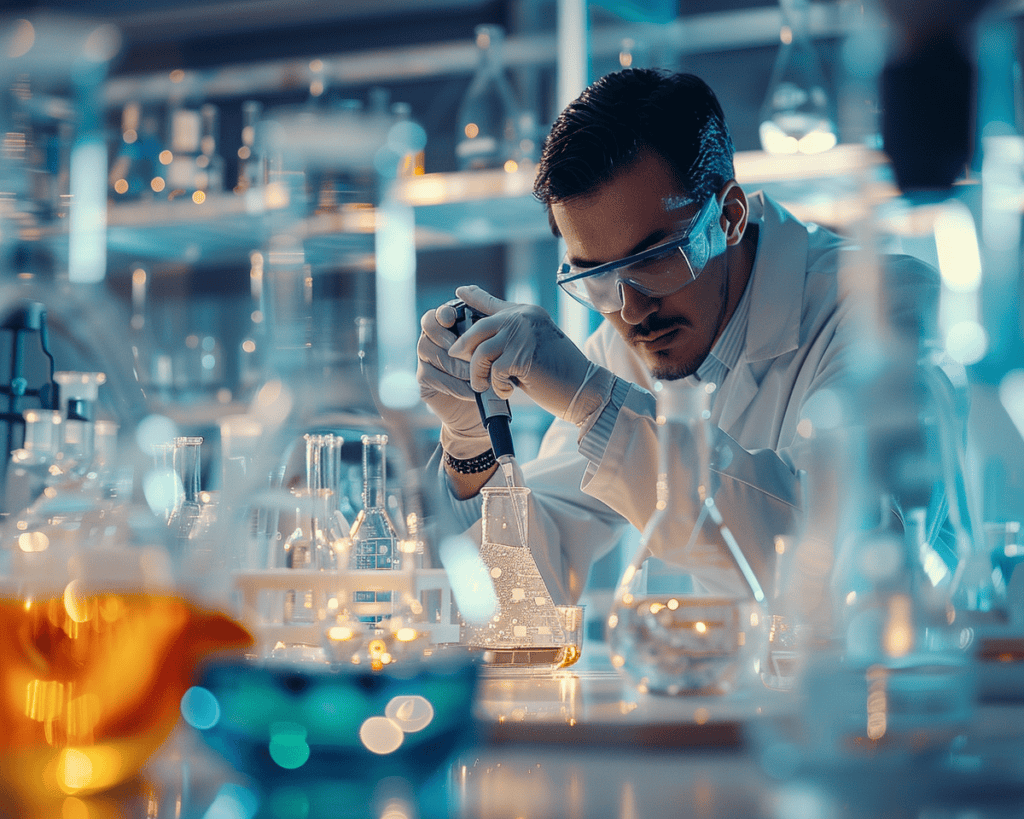
Challenges in Process Development
Process development is not without its challenges. One of the biggest hurdles is ensuring that the process is scalable. A method that works perfectly in the lab might not be as effective when applied to large-scale production. There’s also the challenge of meeting strict regulatory requirements. The pharmaceutical industry is one of the most heavily regulated industries in the world, and for good reason. A single mistake in the process can lead to harmful side effects or even death.
But that’s not all. There’s also the challenge of cost. Developing a new drug is incredibly expensive, and the process development stage is no exception. Pharmaceutical companies must balance the need for a high-quality product with the need to keep costs under control. It’s a delicate balancing act, and one that requires a lot of expertise and experience.
The Future of Process Development
Looking ahead, what does the future hold for process development? Advances in technology are already changing the landscape. Automation, artificial intelligence, and machine learning are being integrated into the process development stage, making it faster and more efficient. These technologies can help identify potential problems early on, reducing the risk of costly errors later in the process.
Moreover, the trend toward personalized medicine is also influencing process development. In the past, drugs were developed with the idea that one size fits all. But as we learn more about genetics and individual responses to medication, there’s a growing demand for drugs tailored to the individual. This shift is challenging traditional process development methods, pushing scientists to innovate and adapt.
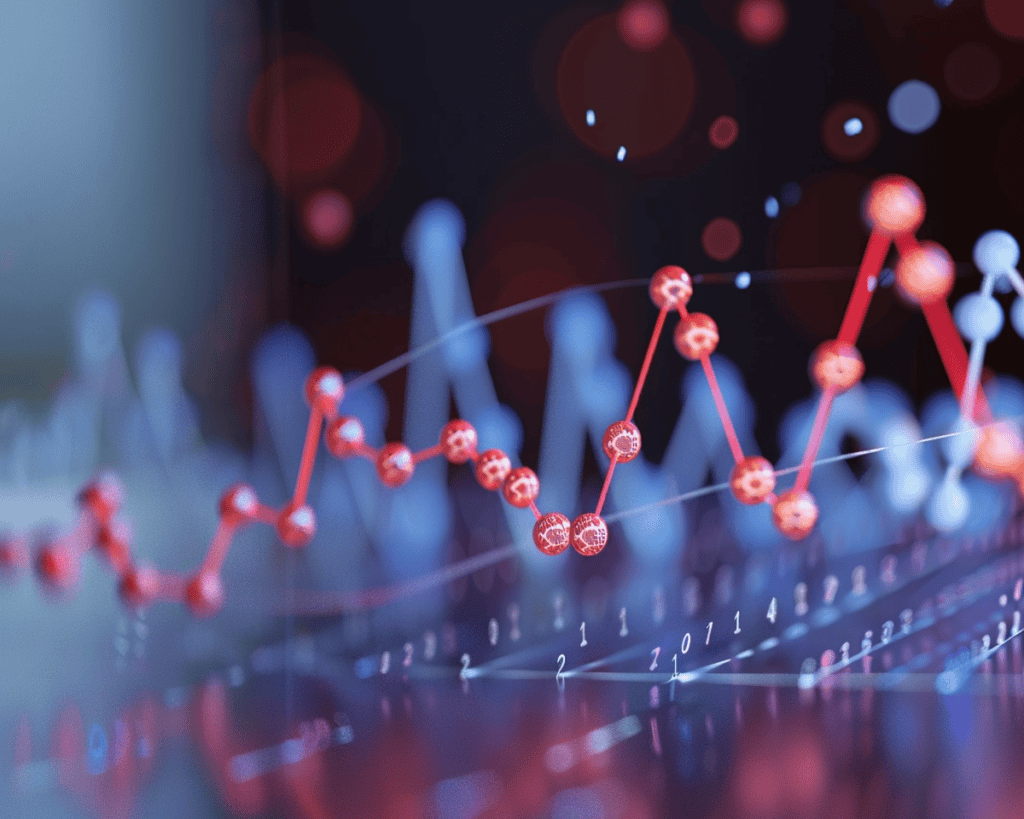
Conclusion
So, what do you think? Process development might not be the most glamorous part of drug production, but it’s undoubtedly one of the most important. It’s the backbone of the pharmaceutical industry, ensuring that the medicines we take are safe, effective, and reliable. Without it, the drugs we rely on every day simply wouldn’t exist.
Next time you take a pill, consider the journey it took to get to you. Behind that tiny tablet is a world of science, engineering, and meticulous planning. And all of it starts with process development—a critical step that turns a simple idea into life-saving medication.