Introduction: Importance of Pump Maintenance for System Longevity
Your HPLC pump is the heart of your chromatography system. It delivers the mobile phase at a precise and stable flow rate, ensuring accurate retention times, reproducible peak areas, and overall system performance. However, if not properly maintained, your pump can become a major source of pressure fluctuations, leaks, and flow inconsistencies, leading to costly downtime and unreliable results.
Neglecting pump maintenance can lead to damaged seals, clogged check valves, and erratic flow rates, significantly reducing the lifespan of your system. Fortunately, routine cleaning, timely part replacements, and solvent management can keep your pump in peak condition for years.
In this guide, we’ll cover:
✔ Common issues and their causes
✔ Routine cleaning and flushing techniques
✔ How to inspect and replace seals and pistons
✔ How solvent choice affects pump performance
✔ Troubleshooting pressure-related pump failures
By following these best practices, you can extend the life of your HPLC pump, improve system reliability, and reduce maintenance costs.
1. Common Issues with HPLC Pumps and Their Causes
HPLC pumps are high-precision mechanical components, and even minor issues can lead to serious performance problems. Here are the most common pump failures and their underlying causes:
1.1 Pressure Fluctuations
🚩 Symptom: Unstable baseline, retention time shifts, or sudden pressure drops.
🔹 Causes:
- Leaky pump seals allowing air to enter the system.
- Partially clogged inlet filters or frits restricting solvent flow.
- Degasser malfunctions causing bubble formation.
1.2 Pump Seal Wear and Leaks
🚩 Symptom: Solvent leaks from pump head or inconsistent flow rate.
🔹 Causes:
- Aging pump seals degrade over time, especially with harsh solvents.
- Dry running the pump can cause premature seal failure.
- Improper solvent compatibility accelerates seal deterioration.
1.3 Check Valve Malfunctions
🚩 Symptom: Flow rate inconsistencies or complete pump failure.
🔹 Causes:
- Salt buildup from buffers restricting valve movement.
- Mobile phase impurities causing valve sticking.
- Wear and tear from repeated solvent exposure.
1.4 Flow Rate Instability
🚩 Symptom: Variable retention times and irreproducible peak areas.
🔹 Causes:
- Air bubbles trapped in the pump head disrupting solvent flow.
- Inconsistent mobile phase composition affecting viscosity.
- Improper pump calibration leading to incorrect flow settings.
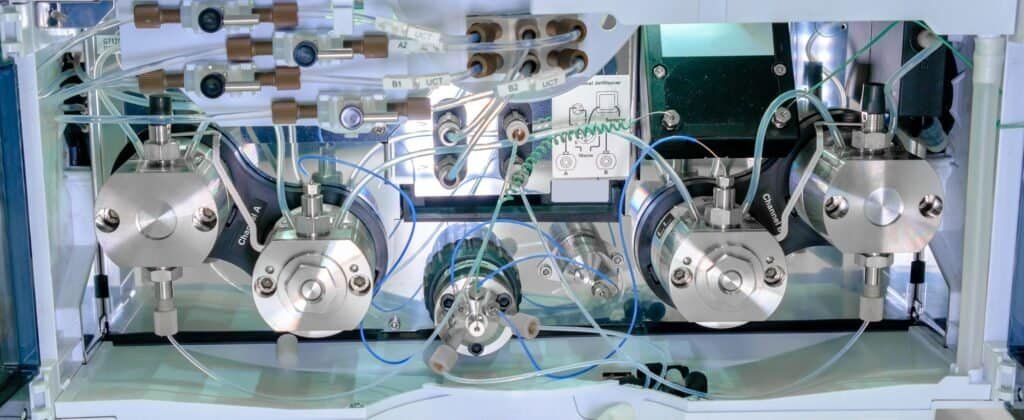
If you’ve ever dealt with unpredictable flow rates or unexplained pressure drops, chances are your pump needs maintenance. Let’s look at routine cleaning and flushing techniques to prevent these issues.
2. Routine Cleaning and Flushing Techniques
Regular cleaning of your HPLC pump components prevents blockages, contamination, and premature wear.
2.1 When to Flush Your Pump
✔ Daily: If using buffers or high-salt mobile phases, flush with HPLC-grade water at the end of the day.
✔ Weekly: If running organic solvents, flush with a weaker solvent (e.g., methanol before water).
✔ Monthly: Perform a deep clean with alternating solvent flushes.
2.2 How to Flush the HPLC Pump Properly
🔹 Step 1: Disconnect the column to prevent contamination buildup.
🔹 Step 2: Run HPLC-grade water for 5–10 minutes to remove salts and buffer residues.
🔹 Step 3: Follow with isopropanol or methanol to clear organic deposits.
🔹 Step 4: If heavy contamination is suspected, flush with 50:50 methanol/water + 0.1% formic acid.
🔹 Step 5: Reconnect the column and allow equilibration before resuming normal operation.
Pro Tip: Never leave buffers or aqueous solutions sitting in the system overnight—they promote microbial growth and salt precipitation!
3. Best Practices for Checking Pump Seals and Pistons
The pump seals and pistons are responsible for maintaining a leak-free and airtight system. Damaged seals cause pressure drops, air bubbles, and solvent leaks.
3.1 Signs Your Pump Seals Need Replacing
✔ Sudden pressure fluctuations or retention time shifts.
✔ Solvent leaks near the pump head.
✔ Decreased flow rate despite normal pump settings.
3.2 Replacing Worn Pump Seals
🔹 Step 1: Shut down the system and depressurize the pump.
🔹 Step 2: Remove the pump head using the manufacturer’s instructions.
🔹 Step 3: Carefully remove the old seals using a seal removal tool.
🔹 Step 4: Install new, solvent-compatible seals, ensuring proper alignment.
🔹 Step 5: Reassemble the pump and run a low-pressure solvent flush to check for leaks.
Pro Tip: Inspect pistons for scratches or buildup—damaged pistons accelerate seal wear and should be replaced when necessary.
4. How Solvent Choice Affects Pump Performance
Did you know that your choice of mobile phase solvents can extend or shorten the lifespan of your pump? Some solvents are more aggressive than others and can degrade pump components faster.
4.1 Using Solvent-Compatible Pump Seals
✔ PTFE (Teflon) Seals – Good for organic solvents, but not for aqueous buffers.
✔ PEEK Seals – More resistant to acids and bases, making them ideal for buffered systems.
✔ UHMWPE Seals – Best for harsh solvents, but wear out faster.
4.2 Solvent Properties That Impact Pump Life
🚩 High-Salt Buffers: Precipitate over time, leading to check valve blockages.
🚩 pH Extremes (Below 2 or Above 10): Can corrode metal pistons and seals.
🚩 Halogenated Solvents (e.g., Dichloromethane): Cause swelling in standard pump seals.
🚩 High-Viscosity Solvents (e.g., DMSO): Strain the pump motor, reducing longevity.
4.3 Preventing Solvent-Related Pump Damage
✔ Use filtered, degassed solvents to prevent air bubbles.
✔ Choose compatible seal materials based on mobile phase composition.
✔ Flush the system regularly to remove residues and prevent precipitation.
5. Troubleshooting Pressure-Related Pump Failures
Pressure issues are among the most common pump-related problems in HPLC. Here’s how to diagnose and fix them:
5.1 High-Pressure Spikes
🔹 Cause: Blocked frits, tubing, or column.
🔹 Fix:
✔ Disconnect the column and see if pressure drops.
✔ Flush the system with strong solvents to clear blockages.
5.2 Low or Fluctuating Pressure
🔹 Cause: Leaky pump seals or air bubbles.
🔹 Fix:
✔ Check tubing connections for loose fittings.
✔ Replace worn-out pump seals and degas solvents.
5.3 Pump Not Delivering Solvent
🔹 Cause: Faulty check valves or clogged inlet filters.
🔹 Fix:
✔ Clean or replace check valves.
✔ Ensure mobile phase bottles are full and the pump is primed.
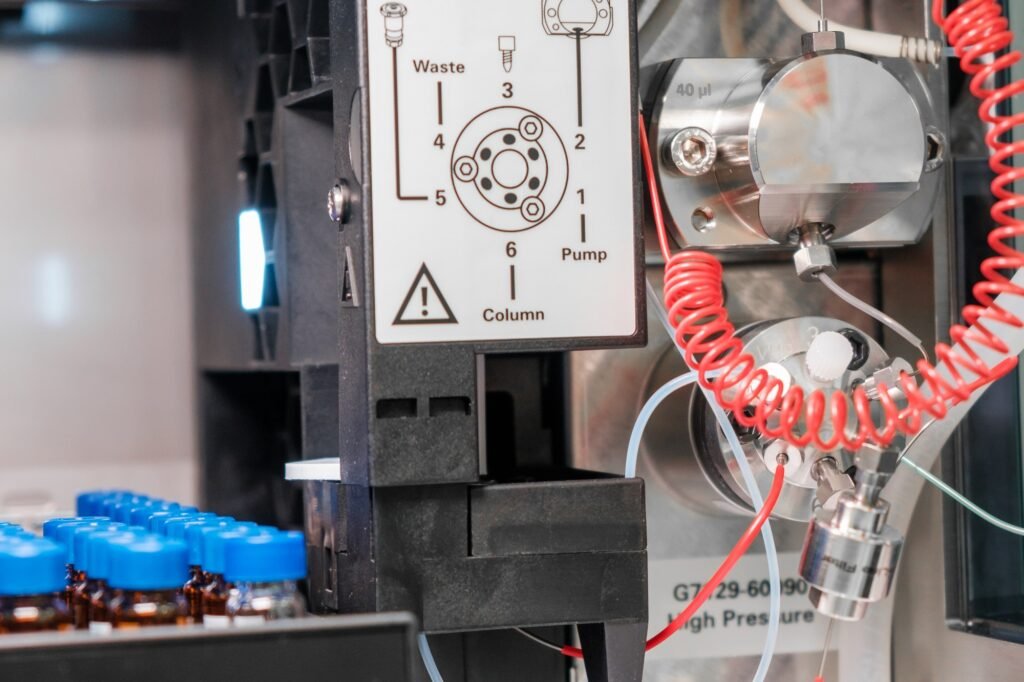
Conclusion: Adopt a Pump Maintenance Schedule
By following a regular pump maintenance schedule, you can extend the life of your HPLC system, reduce downtime, and improve data reliability.
✔ Daily – Flush with fresh solvent at the end of each run.
✔ Weekly – Check pump seals for leaks and inspect tubing.
✔ Monthly – Perform a deep clean with strong solvents.
✔ Every 6 Months – Replace pump seals, check valves, and pistons.
Your HPLC pump is a long-term investment—taking care of it ensures years of reliable performance. Start implementing these maintenance practices today and prevent unexpected failures in the lab! 🚀
Mastelf, with over 13 years of experience in chromatography vials, we can help you find the exact vials you need for your applications.
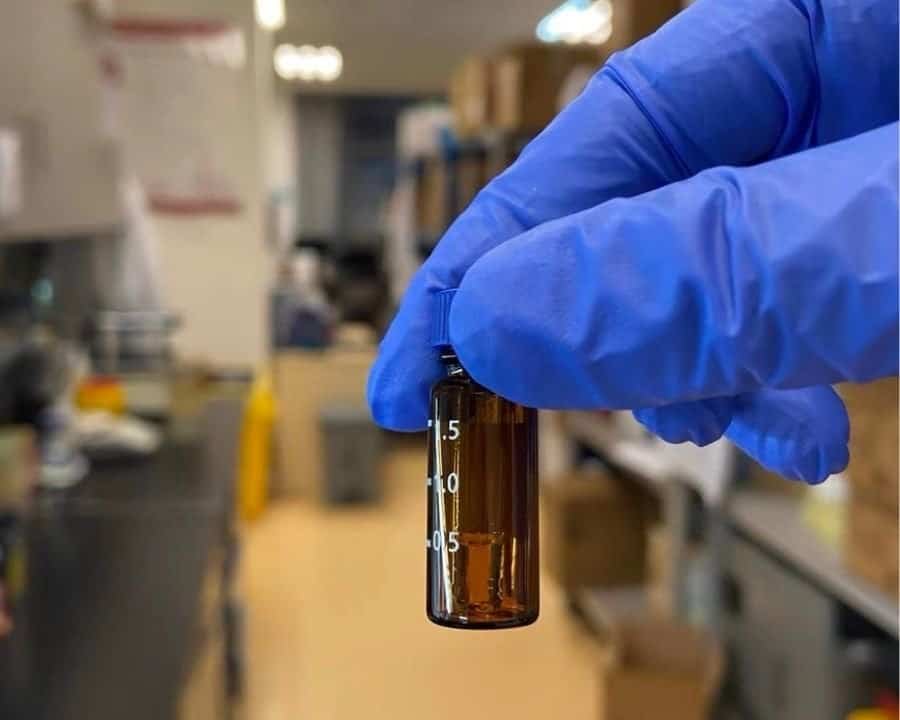
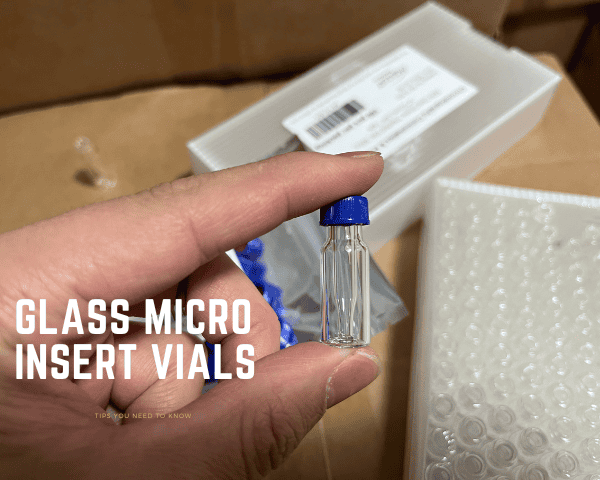
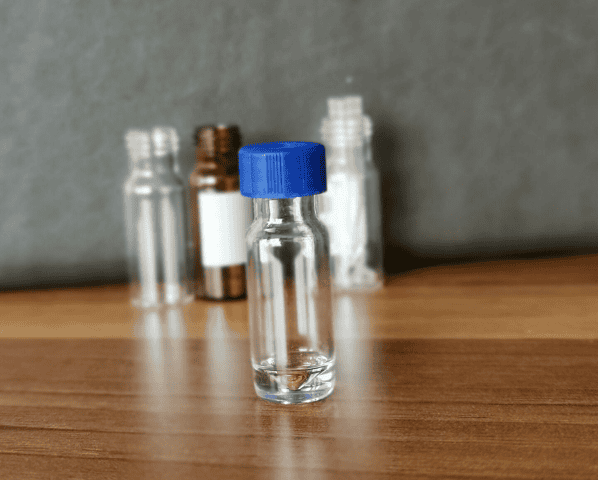
Our expertise ensures that you get reliable and precise products tailored to your specific requirements. Whether you’re in pharmaceuticals, research, or any other industry relying on HPLC, we understand your needs and are here to support you in making the right purchase.
Reach out to Mastelf, and let us assist you in procuring the perfect vials for your work.
FAQs
1. How often should I replace HPLC pump seals?
Every 6–12 months, depending on solvent use and system pressure.
2. What’s the best solvent for flushing my pump?
Use HPLC-grade water for aqueous systems and methanol or acetonitrile for organic solvents.
3. Why does my HPLC pump keep losing pressure?
Check for air bubbles, worn seals, or leaks in tubing connections.
4. Can I run my HPLC pump dry?
No! Dry running damages pump seals and pistons. Always keep mobile phase bottles filled.
5. How can I prevent salt buildup in my pump?
Flush with water daily if using buffered mobile phases.