When you think of quality glass, what comes to mind? Most likely, it’s clarity, strength, and durability. Whether you’re manufacturing glass for windows, bottles, or scientific equipment, ensuring the quality of the glass is crucial to prevent defects that could compromise safety or function. If you’ve ever wondered how professionals inspect glass for quality, I’ve got just the thing for you. Let’s walk through the key steps involved in a thorough glass quality inspection.
Why Does Glass Quality Matter?
Before diving into the inspection process, let’s take a second to understand why quality matters so much in the glass industry. The most obvious reason is safety. Faulty glass can lead to accidents, especially in critical applications like construction or in labs. Ever considered how catastrophic a lab explosion could be if the glassware was subpar? Additionally, imperfections in glass can affect performance, such as causing distortions in optical glass or contaminating products in pharmaceutical vials. So, inspecting glass isn’t just about finding cracks—it’s about ensuring functionality and safety.
But what do you think? Would you feel comfortable using glass if you knew it hadn’t been inspected thoroughly? Probably not.
The Basics of Glass Quality Inspection
Visual Inspection
The first step in any glass quality inspection is a good, old-fashioned visual check. This might sound simple, but it requires a sharp eye and attention to detail. A visual inspection helps identify any obvious defects like:
- Cracks or Chips: No one wants a glass window or bottle with visible cracks. These are the most common defects and the easiest to spot.
- Air Bubbles: Trapped air during the manufacturing process can create small bubbles in the glass, which compromise its strength.
- Surface Scratches: Even the smallest scratches can weaken glass, especially if it’s going to be used in high-stress environments like construction.
What’s interesting is that these visible flaws are often a sign of deeper structural problems, which is why spotting them early is so important. Don’t you agree?
Light Transmission and Refraction Tests
One method used for glass inspection is light transmission and refraction testing. This technique checks whether the glass allows light to pass through evenly without distortion, which is essential for products like lenses and windows.
For this test, a light source is directed at the glass, and the way the light behaves is observed. Any bending or distortion indicates imperfections inside the glass. This method is especially important in industries where clear, undistorted vision is necessary, such as the optical or automotive sectors.
Measurement and Thickness Verification
Glass needs to meet exact specifications for thickness, especially when it’s being used in products like windows or laboratory equipment. Too thin, and it’s more prone to breaking; too thick, and it may not fit properly in the intended frame or holder.
Measuring tools like micrometers or laser thickness gauges are commonly used in this step. Consistent thickness ensures that the glass will be durable and fit its purpose.
Surface Finish Analysis
Surface finish analysis is another critical aspect of glass inspection. This is where inspectors check for texture consistency, smoothness, and any rough edges. In industries where aesthetics are important, such as in high-end glassware, this step helps ensure that the glass looks as good as it performs.
Advanced Testing Methods for Glass Quality
Stress Analysis
Glass, while strong, is prone to breaking under stress. Stress analysis helps to ensure the glass can withstand pressure or thermal changes without shattering. How is this done? One common method is using polarized light. When polarized light passes through glass, stress points become visible. This is especially important for safety glass used in car windshields or laboratory equipment, where a sudden break could have dangerous consequences.
There’s also the option of mechanical testing, where controlled pressure is applied to the glass until it breaks. This destructive test helps determine the maximum stress the glass can handle. You might be thinking: isn’t it counterproductive to break glass just to test it? But the information gathered can be invaluable for improving future production.
Thermal Shock Resistance Testing
Glass can expand or contract based on temperature changes, which could cause it to crack. Thermal shock resistance tests expose glass to extreme temperatures to ensure it won’t fail in real-world conditions. This test is crucial for glass used in environments like ovens or freezing temperatures. If the glass passes this test, it’s usually safe for use in any condition.
Imagine a scenario where lab glassware fails to withstand sudden temperature changes during an experiment—disaster, right? That’s why this test is non-negotiable for high-quality glass production.
Hardness Testing
Another way to ensure the durability of glass is by performing hardness tests. These tests determine how well the glass can resist scratching and surface damage. A standard tool for this is the Mohs Hardness Scale, which ranks materials from 1 to 10. Glass typically scores around a 5, meaning it’s quite hard, but still susceptible to certain abrasions.
For even more precision, some manufacturers use indentation testing to measure hardness at a microscopic level, which is particularly useful for specialized glass like that used in electronics.
Automation and Technology in Glass Inspection
Automated Visual Inspection Systems
With advances in technology, more glass manufacturers are turning to automated visual inspection systems. These machines use high-resolution cameras and software to detect flaws much faster than a human inspector could. They are particularly useful for large-scale production lines where human error might let a few defects slip through.
The system scans each piece of glass, compares it to ideal standards, and flags any inconsistencies. Automation has been a game-changer in improving efficiency and reducing waste. I mean, would you trust a robot more than a human for this kind of task? It’s an interesting debate!
X-Ray and Ultrasonic Testing
X-ray and ultrasonic testing are advanced methods used to inspect the internal structure of glass. These tests can identify internal cracks or imperfections that aren’t visible on the surface. X-rays pass through the glass, and any imperfections will appear as shadows, making it easy to detect hidden flaws.
Ultrasonic testing works similarly, using sound waves to detect inconsistencies inside the glass. These techniques are particularly useful in industries that require glass to be flawless, such as pharmaceuticals, where even a tiny defect could contaminate the product.
Mastelf’s Commitment to Quality: COA Reports for Every Batch
One of the key benefits of working with Mastelf is that every batch of products comes with a Certificate of Analysis (COA). This report ensures that the product quality is within strict, controllable limits, allowing you to purchase with confidence. Whether you’re running critical experiments or scaling up production, having a COA gives you the peace of mind that your glassware and other consumables meet high standards, ensuring both laboratory safety and reliable results. Isn’t it comforting to know that your lab equipment is backed by thorough quality control?
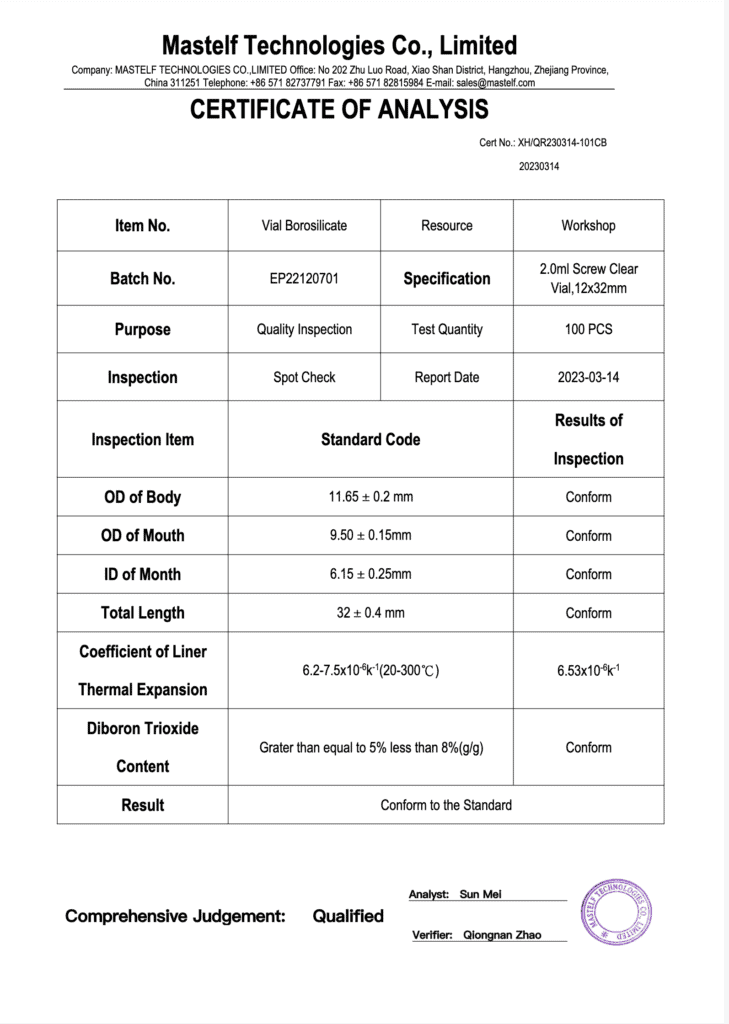
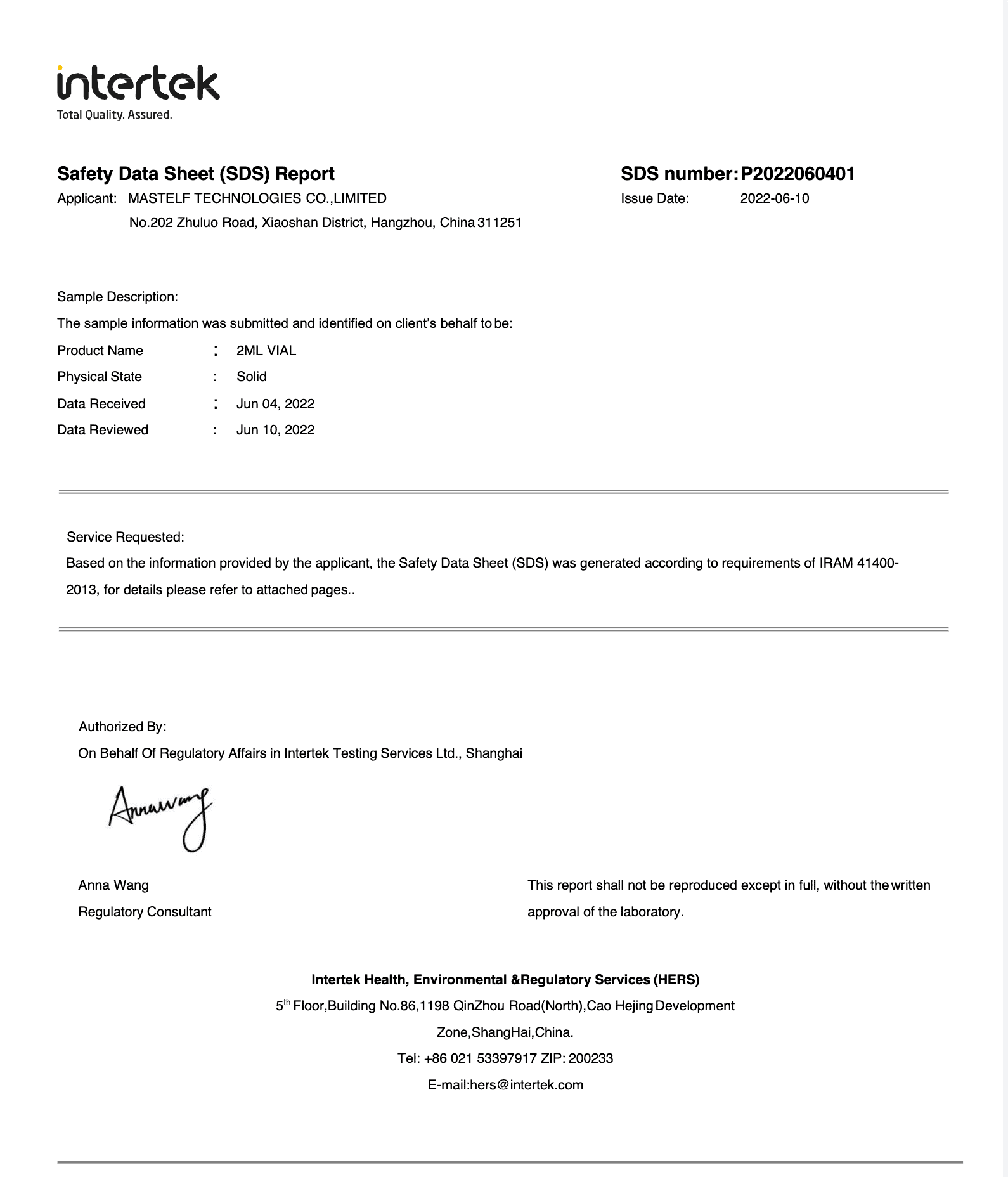
Conclusion: What Does Quality Look Like to You?
Ensuring glass quality is no simple task, but by using a combination of visual inspections, stress tests, and advanced technology, manufacturers can produce glass that is safe, strong, and durable. Whether you’re making lab glassware or windows for skyscrapers, these inspection methods will give you peace of mind that your glass is up to standard.
What do I think? I believe quality inspection is one of the most critical stages in glass production. It saves money, ensures safety, and boosts customer satisfaction. What about you—do you think quality is more about safety or aesthetics?
Sources:
- Glass Magazine: Best Practices in Glass Inspection
- Springer: Thermal Shock Resistance Testing
- Wiley: Stress Analysis in Glass Manufacturing