Introduction
You see them everywhere—those simple yet essential PP (Polypropylene) caps on bottles, vials, and containers. But have you ever thought about what goes into making them? The production process of PP caps is pretty fascinating, blending technology, precision, and quality checks. Let’s break it down together. Sound interesting? Let’s dive in.
Answer Section
The production process of PP caps involves multiple stages including material preparation, injection molding, cooling, trimming, and quality inspection. Each step plays a crucial role in ensuring the final product is reliable and meets industry standards.
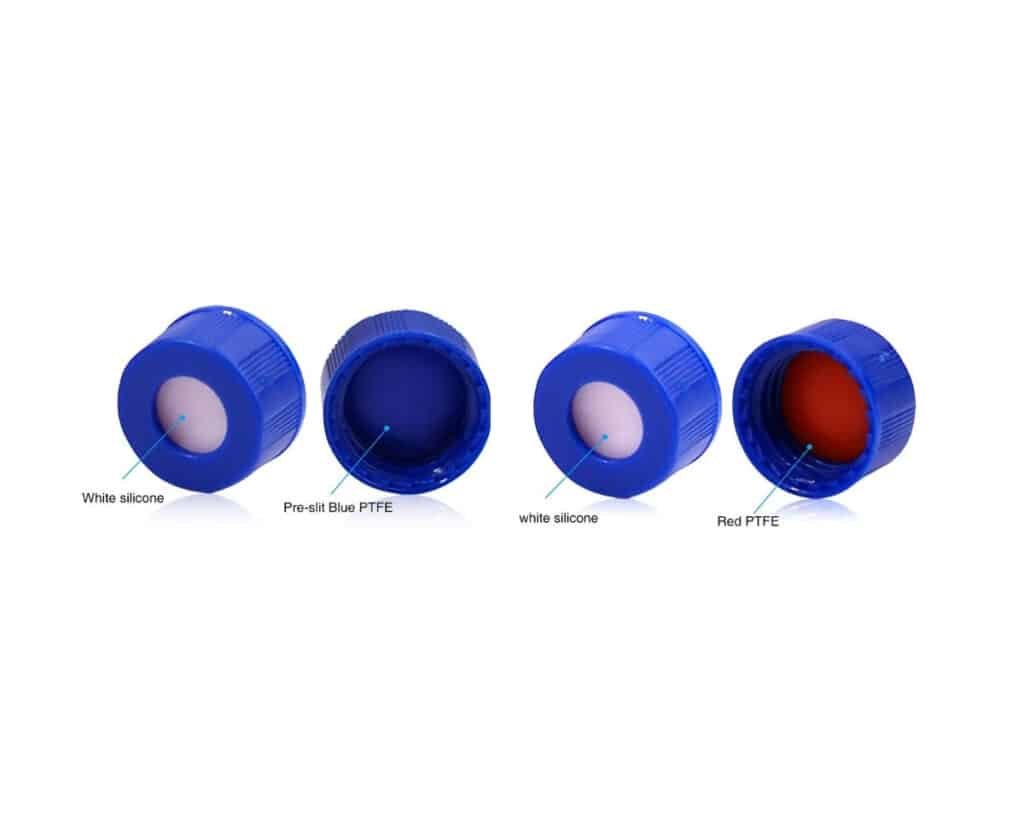
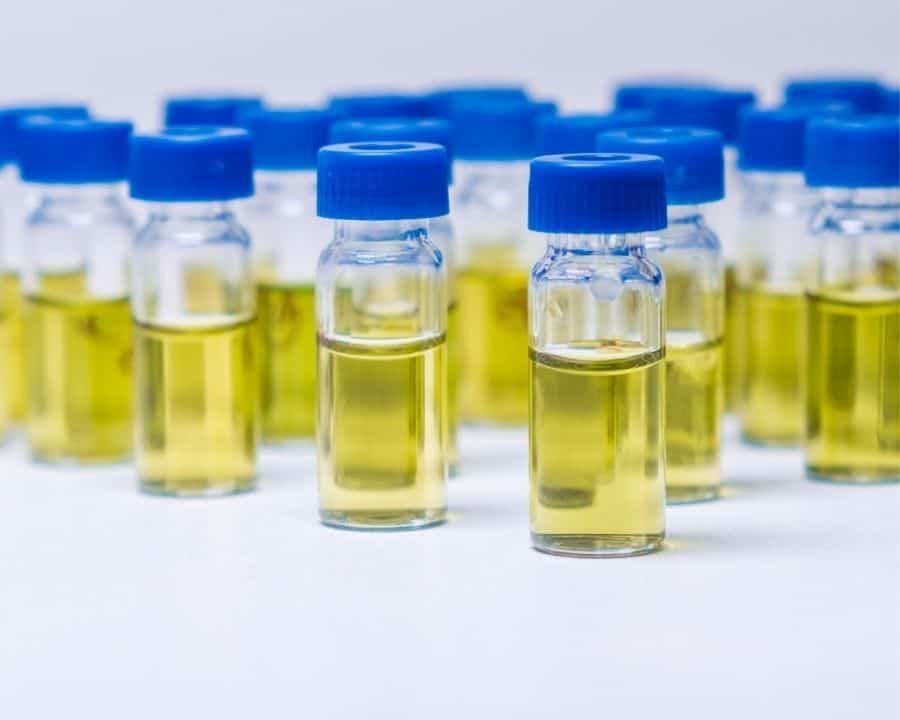
Raw Material Selection and Preparatio
Why Polypropylene (PP)?
Polypropylene (PP) is often the material of choice for manufacturing caps, containers, and other consumables, and it’s not without reason. But how does it compare to other common plastics like ABS (Acrylonitrile Butadiene Styrene) and PE (Polyethylene)? Let’s dive into a comparison to understand the strengths and weaknesses of each.
Polypropylene (PP) – Strengths and Weaknesses
Polypropylene is a versatile and lightweight plastic known for its chemical resistance and thermal stability. It’s particularly well-suited for applications like bottle caps, lab vials, and automotive parts because it resists chemicals and solvents, which is essential in scientific applications. PP also has a relatively high melting point, around 160°C (320°F), allowing it to handle higher temperatures without deforming.
On the downside, PP isn’t as rigid as some other plastics. It can become brittle at low temperatures, which might be a concern in very cold environments. Also, while it’s resistant to many chemicals, it doesn’t have the same toughness or impact strength as some other plastics.
Acrylonitrile Butadiene Styrene (ABS) – Tough but Expensive
ABS is known for its toughness and impact resistance. If you’ve ever played with LEGOs, you’ve experienced ABS firsthand! It’s great for applications where durability and rigidity are key. For example, ABS is often used in automotive parts, electronic housings, and even toys.
However, ABS is more expensive than PP and not as chemically resistant. It can also struggle with UV exposure and higher temperatures, making it less ideal for outdoor applications or situations where chemical exposure is a factor. So, while it’s great for making robust items, ABS doesn’t offer the same flexibility and chemical resistance that PP does.
Polyethylene (PE) – Versatile but Limited in High Temps
PE comes in several varieties, including Low-Density Polyethylene (LDPE) and High-Density Polyethylene (HDPE). HDPE is quite strong and is often used for heavy-duty containers, while LDPE is more flexible and used for films or bags.
PE offers excellent moisture resistance, making it a popular choice for packaging. However, it doesn’t handle heat as well as PP. Its melting point ranges from 110-130°C (230-266°F), which is lower than PP’s. This means that in applications involving heat, PP is a more reliable option. Furthermore, while PE is resistant to many chemicals, it doesn’t have the same structural integrity for mechanical applications as ABS or PP.
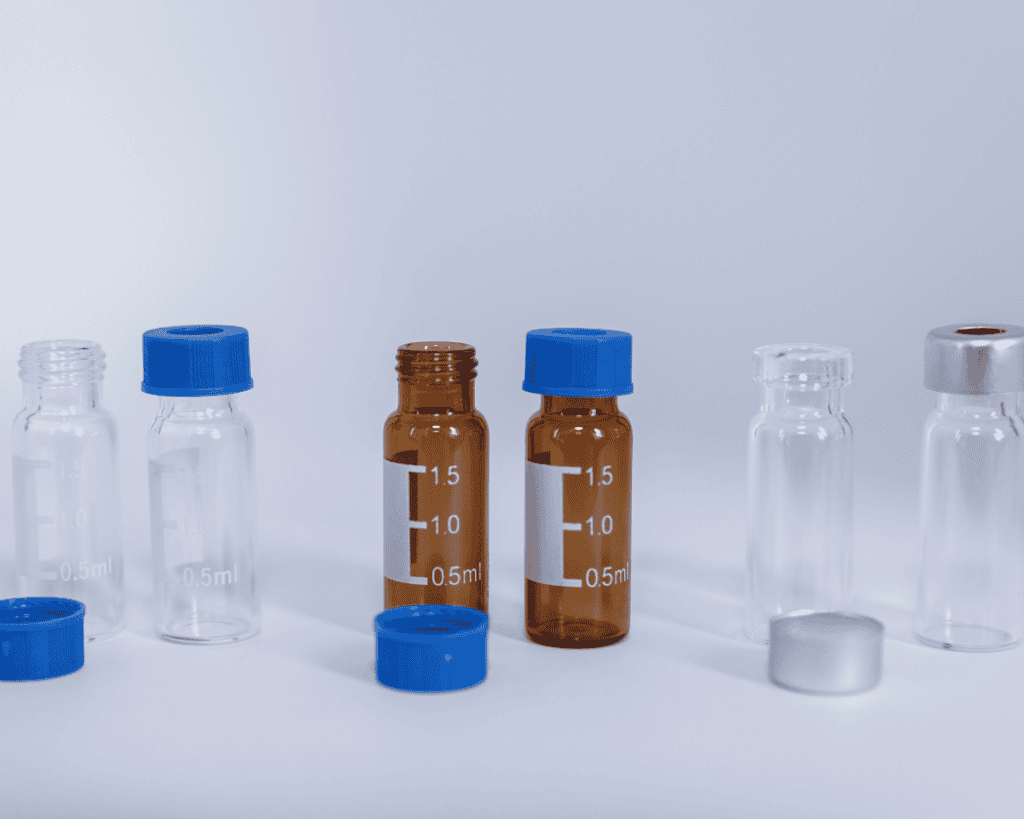
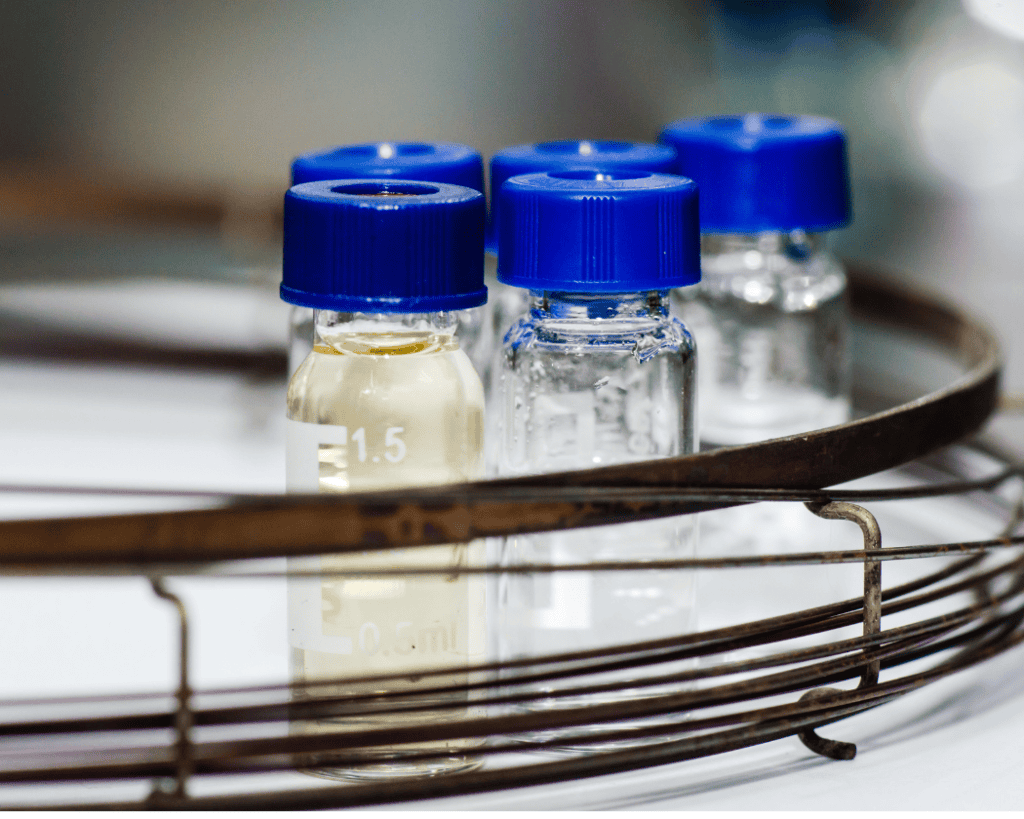
Want more details on these plastics? Check out this in-depth guide from Plastics Europe.
How Does PP Compare Overall?
When you put them all together, PP shines because of its balance of cost-effectiveness, chemical resistance, and thermal stability. It’s not as tough as ABS or as moisture-resistant as PE, but it’s versatile and works well in a variety of situations, especially where chemical exposure and heat resistance are required.
So, what’s the takeaway? Choosing the right plastic depends on the application. Do you need impact resistance and rigidity? Go for ABS. Moisture resistance? PE might be the way to go. But if you’re looking for a good all-around performer, especially in labs or packaging applications, PP has the edge.
Melting and Material Preprocessing
Before the production starts, raw PP material is loaded into a hopper and heated until it melts. This process turns the solid granules into a viscous, moldable liquid. Temperature control here is key; too much heat, and you risk degrading the material, too little, and it won’t flow well into the molds.
Injection Molding Process
Injecting the Molten PP into Molds
Once the PP material is melted and ready, it’s injected into pre-designed molds using high-pressure injection molding machines. The mold design determines the cap’s shape, dimensions, and features. For instance, caps with threads or unique sealing ridges require precisely engineered molds.
Cooling and Solidifying
After the injection, the molds are cooled using water channels to solidify the cap. Cooling time needs to be just right—not too fast to avoid warping, and not too slow to maintain productivity. This step gives the caps their final shape and strength.
Removing Caps from the Molds
Once cooled, the caps are automatically ejected from the molds. Automation is crucial here to maintain speed and avoid human error. Imagine manually pulling out thousands of tiny caps every hour!
Trimming and Finishing
Removing Excess Material
In this stage, any excess or “flash” material is trimmed off the caps. Automated systems or trimming machines are typically used for efficiency. Quality control teams then inspect the caps to ensure the edges are smooth and free from imperfections that could impact the sealing.
Want to learn more about automated trimming? Check out this technical guide on automation in manufacturing.
Adding Special Features or Branding
Some caps require additional features like sealing liners or embossing with brand logos. This can be achieved using specialized machinery that inserts liners or stamps designs onto the caps. It’s a crucial step for brands that want to establish a strong market presence.
Quality Control and Testing
What’s the point of a perfectly molded cap if it can’t seal properly or is easily damaged? At this stage, each batch of caps undergoes rigorous testing for durability, tightness, and resistance to chemicals. Various tests are conducted to ensure they meet the required standards like USP or ISO certifications.
For industry-standard testing guidelines, refer to ISO’s official site.
Packaging and Distribution
Efficient and Protective Packaging
Once the caps are approved, they’re packaged carefully to avoid contamination or damage during transportation. High-quality packaging ensures the caps reach their destination in perfect condition, ready to be used in bottling lines.
Managing Logistics and Distribution
Distribution involves coordinating with logistics providers to get the product safely and timely to clients. Managing this efficiently ensures that your customers receive their orders without delay, which in turn builds trust and loyalty.
Providing After-Sales Support
Here’s an often-overlooked part: after-sales support. Whether it’s providing technical advice or addressing concerns quickly, having a robust support system keeps customers happy and coming back.
Conclusion
When it comes to choosing materials for manufacturing, understanding the strengths and weaknesses of different plastics like Polypropylene (PP), Acrylonitrile Butadiene Styrene (ABS), and Polyethylene (PE) is crucial. PP stands out due to its excellent chemical resistance, heat stability, and cost-effectiveness, making it ideal for lab consumables, packaging, and automotive applications.
In contrast, ABS offers superior toughness and impact resistance, but it’s more expensive and less chemically resistant. PE, on the other hand, excels in moisture resistance but falls short in heat tolerance compared to PP.
Ultimately, the choice of material depends on the specific requirements of each application, with PP being a versatile and reliable option for many industries. Understanding these differences helps in making smart decisions when designing and manufacturing products. Curious about which material fits your needs best?
Fianlly, if you’re on the lookout for high-quality HPLC vials at sensible pricing, you won’t miss out Mastelf. With over 13 years of experience in chromatography vials, we can help you find the exact vials you need for your applications.
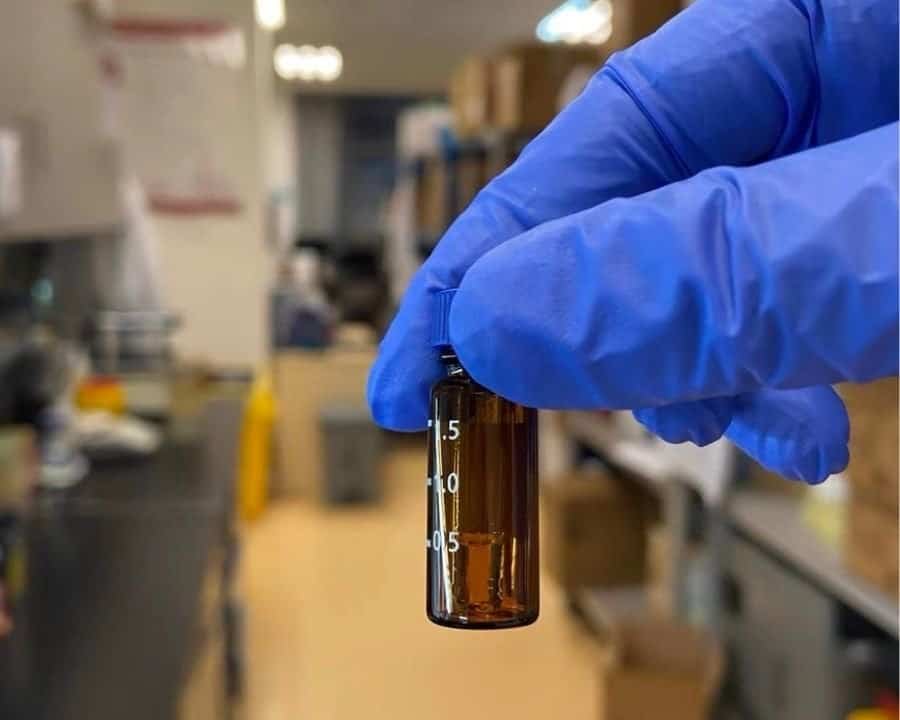
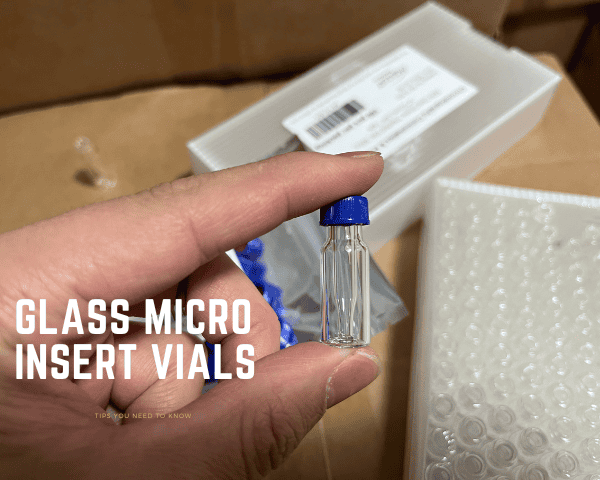
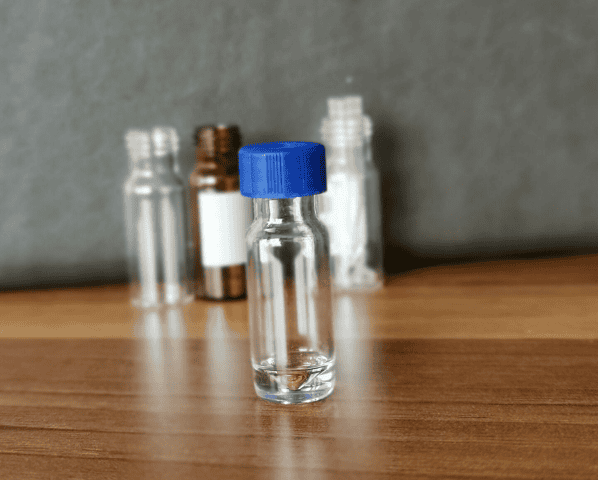
Our expertise ensures that you get reliable and precise products tailored to your specific requirements. Whether you’re in pharmaceuticals, research, or any other industry relying on HPLC, we understand your needs and are here to support you in making the right purchase.
Reach out to Mastelf, and let us assist you in procuring the perfect vials for your work.